Additive Manufacturing (AM) or 3D-printing is a manufacturing process based on the addition of material layer-by-layer to where it is needed based on a CAD-geometry, as opposed to subtractive manufacturing where material is removed from a block of material to carve out the desired geometry.
Laser powder bed fusion (L-PBF) is the most utilized additive manufacturing method for processing metals. The part is built by spreading a thin layer of powder onto a powder bed, which is then selectively melted using a laser to fuse together the metal powder as defined by a 2D-cross section of the CAD-model. After one layer, the building platform is lowered and the cycle repeated until the three-dimensional part is finished.
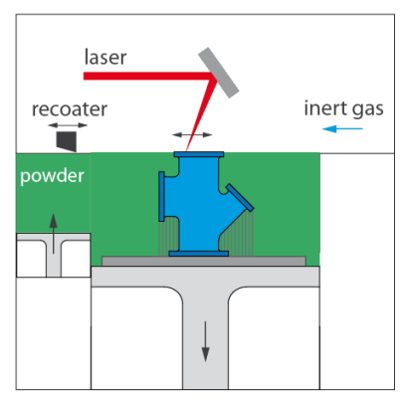
Figure 1 : Principle of additive manufacturing by LPBF
The application of L-PBF for Nd-Fe-B magnets requires careful optimisation of the processing parameters for the given alloy composition to reach the desired microstructure with excellent magnetic properties and dense parts that can withstand the mechanical loads of the application. The brittle nature of the Nd-Fe-B material poses an extra challenge compared to the structural materials (steels, aluminium, titanium) typically processed with L-PBF.